A mezzanine floor, also known as a raised storage area, is an intermediate floor level constructed between two consecutive floors (or storeys) within a building. In the context of a warehouse, the other two floors are the concrete floor slab and the roof. Space Rescue are mezzanine flooring experts who can fabricate and erect a custom structure for you to expand your storage space and office area. Our mezzanine floors and mezzanine floor kits are only available in Australia.
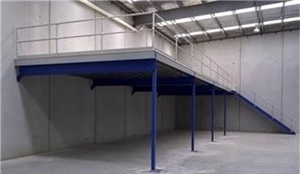
1. Insights
The best flooring material in Australia for a mezzanine level is considered to be tongue & groove structural plywood. The main reasons for this is that plywood is a tough, durable board that offers both great strength in bending and performs well under point loads. A sheet size of 2400mm long x 1200mm wide x 19mm thick is commonly used as it is easy to handle, cost effective and works in well with a 400mm joist spacing.
In Australia, an average mezzanine floor will cost around $330 per square metre. This is based on a structural design with a rating of 300kg per square metre using steel beams and purlins arranged on the most economical grid. This cost excludes both optional accessories and special requirements.
The supply of mezzanine floor kits is an option we consider on a case-by-case basis, as some of our customers are qualified and experienced in erecting this type of structure. Please note that we are able to assemble on site in most capital cities, as well as many surrounding regional areas and towns.
2. Benefits of Mezzanine Floors
A simple solution to your space needs
Mezzanines are a simple yet highly effective means of increasing the floor area within the confines of an existing warehouse by simply adding an additional level.
Less expensive than moving
As mezzanine floor experts, Space Rescue have the ability to design custom floor sizes and shapes to save you the expense in both time and money of having to move to larger premises.
3. Mezzanine Floor Plan
To help you understand the terminology, below is a plan and elevation drawing of a mezzanine floor with a single-level labelled to show the main components. Most of these are steel and consist of structural beams, columns, joists, flooring, and guardrail.
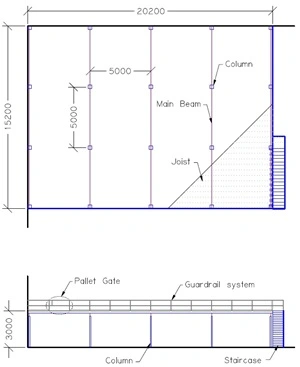
4. Mezzanine Floor Shapes and Configurations
Below are six of the most common and basic mezzanine floor shapes and configurations. Let’s go through them one by one.
Type A is a left-hand corner; Type B is a right-hand corner; Type C is 3-side closed; Type D is 3-side open; Type E is floating; and Type F is a right-angle configuration.
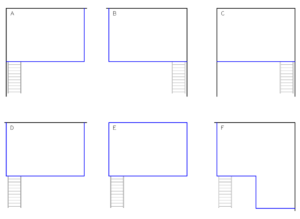
Please note that we are also able to do custom mezzanine shapes.
5. Applications for Mezzanine Floors
a) Storage
A raised storage area (commonly referred to by the acronym R.S.A.) and raised storage platform are two other names used for a mezzanine floor that is specifically designed to create additional storage capacity. The storage of products, stock, and miscellaneous items is the most common use for this raised floor. Pallet jacks and safety pallet gates are necessary for palletised stock. As the pallet jack can exert high point loads, it is important to consider this when selecting the flooring material.
It is not uncommon to use shelving above or below the deck. We recommend the use of longspan shelving or steel shelving on top of the floor. Similar to a pallet jack, it is important to note that shelving can also exert high point loads on the floor surface. This type of mezzanine typically has a higher floor load rating, equal to or greater than 500kg per square meter.
b) Additional Office Space
Conversely, a mezzanine office serves to create extra working, manufacturing or assembly areas in a warehouse or factory unit for personnel. Building offices is possible either above or below the floor level. This can achieved with office style partitions. In this scenario, the partitions would create the necessary fall protection on top of the floor, eliminating the need for a guardrail or handrail system. Designs typically consist of stud walls and a combination of windows and doors. As this a lighter application, it generally has a lesser load rating requirement equal to 300kg per square metre or more.
6. Components of Mezzanine Floors
Mezzanine floor kits contain the following.
a) Columns
Columns (also known as posts) support the steel deck. Posts are almost always square hollow steel sections and are typically around 100mm x 100mm in size. At the upper end of the post are the main beams. The main beams sit directly on top of the posts. A bolted connection secures the post to the beam.
b) Baseplates
The welding of a baseplate at the bottom of a post is common. It consists of a thick square steel flat plate that is typically 300mm by 300mm in size. A baseplate helps spread the load over the concrete slab.
c) Floor anchors to secure Mezzanine Floors
Floor anchors fix the posts to the slab. They anchor into your concrete slab (or concrete footing) with flooring anchors via a baseplate welded at the bottom of the post.
d) Beams
The main beams are the horizontal structural steel members, typically structural I-beams (also known as RSJ’s), that sit on top of the columns or wall brackets. These beams are an essential component, providing support for the flooring joists (and boards in some designs).
e) Joists within Mezzanine Floors
Joists are also horizontal steel members and an essential element in a mezzanine kit. They support the flooring material. Main beams and/or side wall brackets support the joists. We use cold-rolled C-shaped purlins for our joists, made specifically by passing flat galvanised coil steel through a rollformer to form these long sections. They sit either directly on top of or within the depth of the main beams. Joists also sit adjacent to one another with regular spacing. This spacing is typically 400mm from centre to centre. Their orientation is almost always perpendicular to the main beams.
f) Flooring Boards
Flooring boards generally sit immediately on top of the purlins. Self-tapping screws (also known as self-drilling screws) affix the flooring sheets to the purlins. Several different types of floor surfaces are available, depending on your application. These include tongue-and-groove floor boards (commonly industrial particleboard or structural plywood) and an open-style steel grate.
The tongue-and-groove board design has greater strength around the areas where two boards butt up against one another. A PVC tongue joins the two adjacent boards through opposing board edge grooves to stop differential vertical movement. This keeps the floor surface nice and flat, particularly as dynamic loads are moved across its surface.
g) Guardrail systems and Balustrades
Overview
The guardrail system is a simple and very common balustrade arrangement, designed for personnel safety both on and under a mezzanine floor. Their use is common on the side of staircases, stairwells, walkways, catwalks, and exposed raised platform edges to stop people from falling from heights above one metre.
Guardrail specifically consists of a top tubular steel handrail, a tubular steel midrail (a.k.a., knee rail or intermediate rail), and a kickplate (a.k.a., toe plate or toeboard). You must place all three of these elements parallel to the walkway or floor. Steel tubular stanchions support these elements, featuring hollow balls at the handrail and midrail heights. The hollow balls allow the tubular rails to pass through the stanchions. The final stage is to bolt the stanchions to the deck and then weld the rails to the stanchion balls.
Guardrail Design
The top of the handrail must also be between 900mm and 1100mm. Steel tubular rails are generally supplied with a galvanised finish. They are specifically required to be between 30mm and 65mm in external diameter. When in place, the distance between the underside of the knee rail and the top of the flooring board is to be no greater than 560mm. Similarly, the gap between the bottom of the handrail tube and the top of the midrail tube is to be no more than 450mm.
Kick-plates are used at the floor edge within the guardrail system to help prevent objects from falling on personnel accessing the area below. The top of the kickplate needs to be a minimum of 100mm above the floor. When fitted, any gaps between the bottom of the kickplate and the floor must be less than 10mm.
h) Staircases
Staircase design may consist of straight sections, landings, and returns. The positioning of a staircase is often based on the platform size, shape, layout, and operational constraints.
7. Elements and Sizes for Mezzanine Floors
a) Sub-structure options
The substructure is typically assembled from structural steel components (both columns and main beams) as described in type (i) below or pallet racking (end frames and beams) as described in type (ii) below.
i) Structural steel
A structural steel sub-structure supports the deck of Space Rescue’s structural mezzanine floors. It has the advantage of typically being able to offer greater clear spans under your floor and, hence, greater flexibility with the placement of support columns. This creates an opportunity for larger, clearer areas, or more free and open space, to accommodate specific work areas, machinery, and stock movement.
ii) Pallet Racking
A pallet rack or rack-supported floor is often made out of pallet racking components that support the deck, such as frames and beams. Pallet storage and shelving under the deck are common features of this structure.
Extending these frames above the floor level has its advantages. For example, they can be thought of as a ready-made means for including shelving above the floor.
Using pallet racking also has disadvantages, including restricting the layout beneath your raised storage area. Conversely, structural mezzanines require fewer posts. Pallet racking and shelving can still be used under a structurally raised storage area without being part of the structure. This allows for the movement of racking and shelving at any time to accommodate changing needs.
The use of longspan shelving as another sub-structure material is also common. Less common is steel shelving.
b) Deck
The deck surface will consist of either tongue-and-groove flooring boards or mesh decks. Furthermore, beams and joists are also part of the deck sub-structure. The deck height, or the top of the finished floor, is generally between 2.4m and 4.5m.
8. Mezzanine Floor Design
a) Freestanding or Wall Supported
As the name suggests, a freestanding mezzanine structure relies only on the columns for support. It can stand freely without any other supporting aid.
There is often the option in modern warehouses to use adjacent concrete tilt-slab walls (also known as concrete tilt-panels) to support the floors. As a result, this saves money and removes the need for some columns, thus improving the open area under your floor. In this particular case, a bracket, bolted to the wall, supports the floor.
b) Standard or low-profile deck design
To explain, a common deck design consists of the joists laying directly on top of the main beams. In this design it is necessary to weld cleats on top of the supporting beam’s upper flange. Joists bolt on to to these cleats. This is the definition of a top-mount design. The use of this is deeper-profile deck design is common when there is plenty of roof clearance.
Use of a low-profile deck is more frequent when warehouse roof heights are low. Positioning the joists within the profile height of the beam reduces the deck profile height. Here, joists bolt to the beam via side-mount welded cleats. This design positions the top of the joists so that they are at the same height as the top of the beam. Concealing the height of the joist within the often deeper height of the beam considerably reduces the deck profile height. This design technique is often the difference in making the addition of a mezzanine floor viable.
In some situations, it is not possible to place the main beam directly adjacent to a wall. To overcome this, we cantilever joists out from a beam that is positioned away from the wall. This permits the use of a cantilever arrangement with a top-mount design.
c) Beam span and support
There are always a number of ways to support the main beams. This flexibility, along with a variety of beam sizes, dramatically helps us to accommodate the particular needs of our customers. For example, we have the ability to remove central support posts by using larger spans to create clearer areas under the floors.
d) Balustrade design to suit usage
There are two situations that one needs to consider for the design of the balustrades.
Firstly, if the public will be using your floor, you must adhere to more stringent design requirements. For public use, the balustrade cannot have any openings greater than 125 mm. This requirement is to help prevent people, and in particular small children, from falling through them.
Furthermore, if the deck level of the mezzanine is higher than 4 metres, the balustrade must also not have any climbable elements, such as horizontal rails, located between 150 millimetres and 760 millimetres from the floor.
The second situation is when the floor’s use is restricted only to only those working within the organisation. This case permits the use of a simple guardrail design. Please refer to the guardrail section above for more details.
9. Accessories for Mezzanine Floors
Below is a list of common Mezzanine Floor accesories.
a) Access Ladders
An alternative to a staircase is an access ladder. Some of the reasons you would choose an access ladder over a staircase are that they are cheaper and take up less space. Access ladders are not as safe and are a more awkward means of access. Furthermore, ladders are a secondary access option for a staircase.
b) Pallet Gates
Pallet gates consist of either sliding, swinging, or roll-over access. Interestingly, their selection is dependent on budget and operation. Their use makes it possible to transfer palletized loads or cages onto your platform.
c) Pallet Landing Skids
Steel plates protect the mezzanine floors in the area where you deposit and retrieve pallets.
d) Column Protection and Post Protectors
As in pallet racks, column or post protection is available for protecting structural steel columns or uprights within pallet rack-supported floor levels.
e) Catwalks
A raised, horizontal walkway is the definition of a catwalk. A catwalk either connects two platforms together or joins an existing stair landing to a platform.
f) Pallet Jacks
For some raised storage areas, a pallet jack (also known as a pallet truck) will reside on the floor and be required for use. Operators use pallet jacks to position pallets correctly after lifting and placing them on the mezzanine. Similarly, they use the jacks to retrieve pallets and place them near the pallet gate, ready for collection by a forklift.
10. Frequently Asked Questions
The cost of a mezzanine floor is dependent upon the location, size, shape, floor height, floor capacity, number of staircases, access ladders and pallet gates required, post, frame, or wall support, sub-floor design, decking material, and type of deck profile. Generally, prices start from $300 + GST per square metre.
The expense of building a new mezzanine level is relatively low. Many business owners find it an attractive option compared to the price of acquiring additional space or relocating to larger premises.
In Australia, planning permission requirements vary depending on the usage or application, the design and your sites location. We recommend checking with your local council and authorities to help you understand what these local requirements are.
We have been designing, supplying and building mezzanine floors since 2009.
11. Local Help with Mezzanine Floors
Space Rescue has local help available in Sydney, Melbourne, Brisbane, Adelaide, and Perth.
12. Other Products
You may also be interested in our Storage Compactors or Pallet Racking Workbenches?